In accordance with the personal data protection law implemented by the European Union, we are committed to protecting your personal data and giving you control over it. By clicking "Accept All", you allow us to place cookies to enhance your experience on this website, assist us in analyzing website performance and usage, and enable us to serve related marketing content. You can manage your cookie settings below. Clicking "Confirm" means you agree with the current settings.
Factory Line
Let us join hands to achieve manufacturing excellence.
New Product Development Strategy
We closely collaborate with customers from early stages of product development, following high-standard APQP and PPAP processes.
We use scientific simulation analysis for mold design to quickly meet new product demands. Operating under JIT principles for factory planning, we achieve smooth production flow, establish efficient, low-staff production lines, reduce delivery time, and improve competitiveness.
We also actively promote automation, continually improve process capability indicators (Cpk), shorten production cycles, and offer customers high-quality, on-time, and cost-competitive aluminum alloy tubing products.
Mold Design
We offer customized designs based on customer requirements and products, paying close attention to detail and quality to ensure the precision and accuracy of the molds.
Quality Control Tool Inspection
● Vernier Calipers: To confirm the length.
● Fixtures: To confirm the bend and length.
● Inner/Outer Diameter Micrometers: To measure the inner and outer diameters of the tube.
Process Equipment
Annealing Furnace
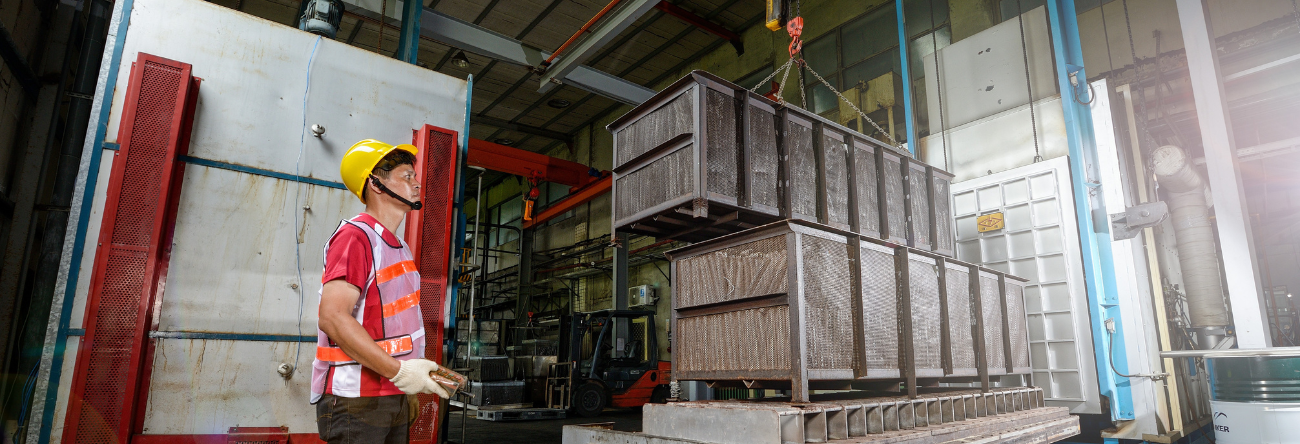
We offer annealing heat treatment services for various aluminum alloy grades, customized to the customer's subsequent processing requirements.
The annealing process for work-hardened aluminum alloy products goes through three stages:
Recovery, recrystallization, and grain growth.
▲Work Hardening: Aluminum alloy products undergo cold working, and as the amount of deformation increases, changes occur in the crystal structure of the material. Increased dislocation density due to deformed and elongated grains enhances the strength and hardness of the product, while its ductility decreases and its plasticity reduces. This phenomenon is known as work hardening or strain hardening.。
▲Stress Relief: To meet further processing requirements, greater external forces must be applied, increasing the risk of product failure.
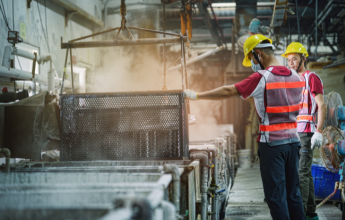
Film Soaping Treatment Equipment (Cleaning / Film)
▲Surface Treatment: It cleans the aluminum alloy surface by removing oxides, grease, and impurities, preparing it for subsequent processing.
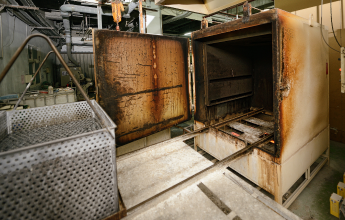
Oven
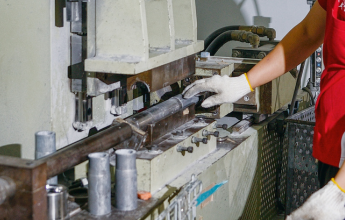
Swaging Machine
Tube Drawing Machine
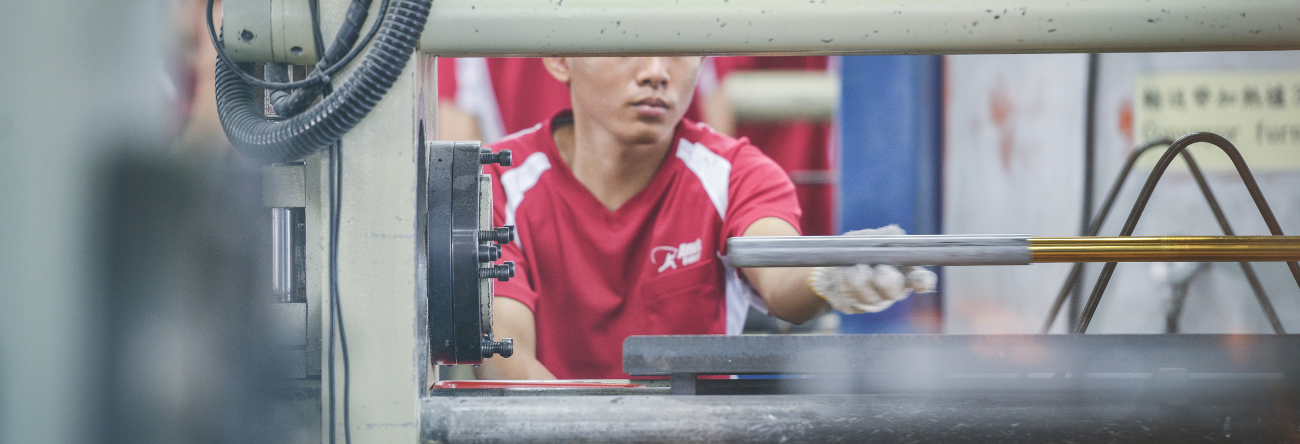
This machine thins the inner wall of the aluminum alloy tube, achieving material lightweight and density strengthening.
The processing can change the shape, size, and thickness of the aluminum alloy tube to meet the needs of different products.
Post-processing aluminum alloy has the characteristics of being efficient, precise, and stable.
Anvil specializes in offering precise aluminum alloy tube drawing, with several tube drawing machines to meet your high-quality mass production needs.
Primary Functions and Applications of the Tube Drawing Machine:
▲Size Adjustment: Through a continuous cold-stretching process, the tube diameter is gradually stretched to meet specific requirements.
▲Shape Adjustment: Allowing the tube shape to be adjusted, like square tubes, octagonal tubes, etc., to adapt to different industrial applications.
▲Precision Improvement: Achieving precision processing, enhancing dimensional accuracy and surface smoothness.
▲Material Adjustment: Altering the structure and material of the tube, improving its mechanical and physical properties.
If special tube drawing dimensions are required, the in-house product's inner and outer diameter tolerance can reach ±0.03mm, with concentricity tolerance within 0.10mm.
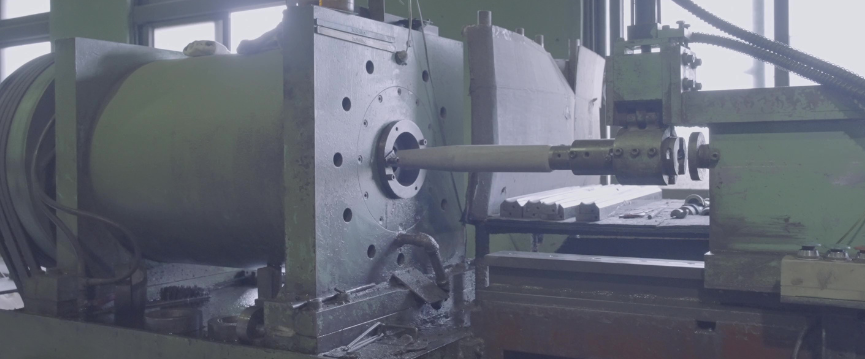
Taper Forming Machine
The purpose is to use linear reciprocating motion to form the tube material into a tapered shape, mainly used to change the shape of the tube material.
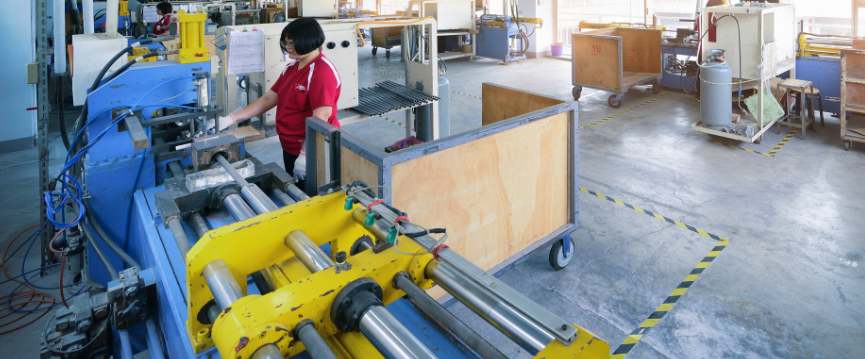
Tube Shrinking Machine
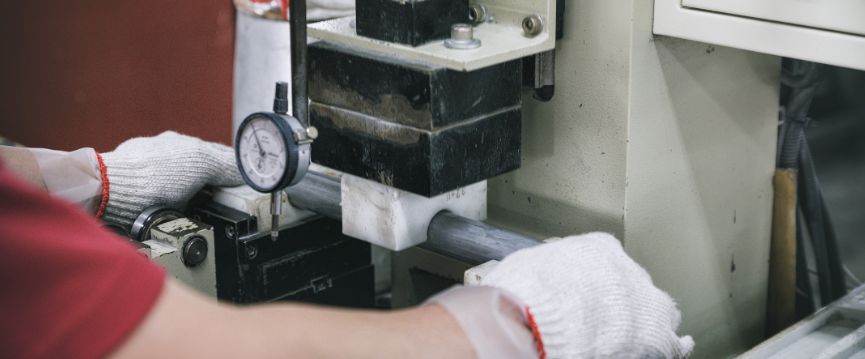
Straightening/Calibration Machine
Oil Hydraulic Forming Machine
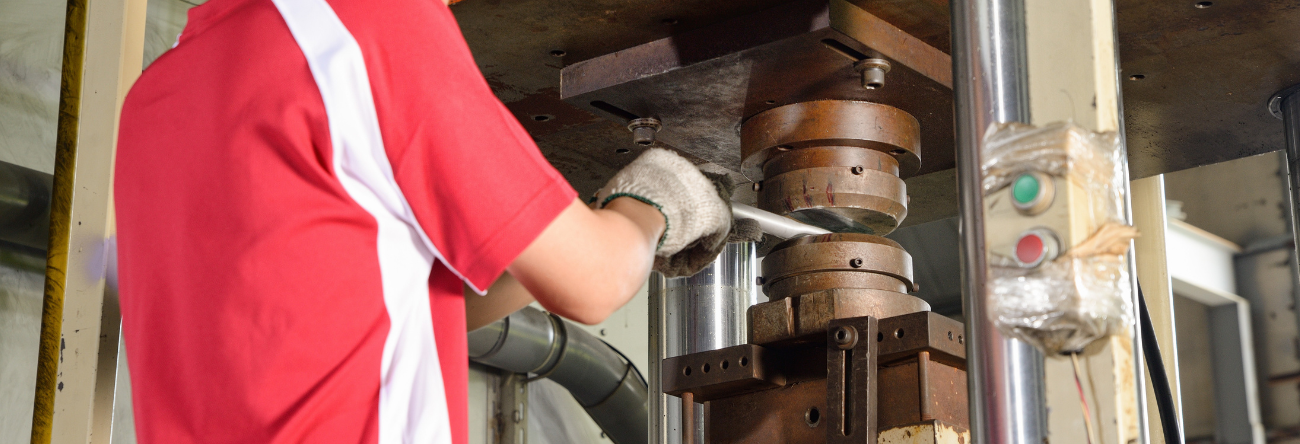
Capable of larger processing capabilities and higher processing pressures, suitable for handling larger, thicker workpieces.
Generally smooth operation with adjustable processing speed and pressure, suitable for applications requiring higher processing intensity and precision.
Punch
Punching Machine
CNC
CNC Automatic Milling Machine
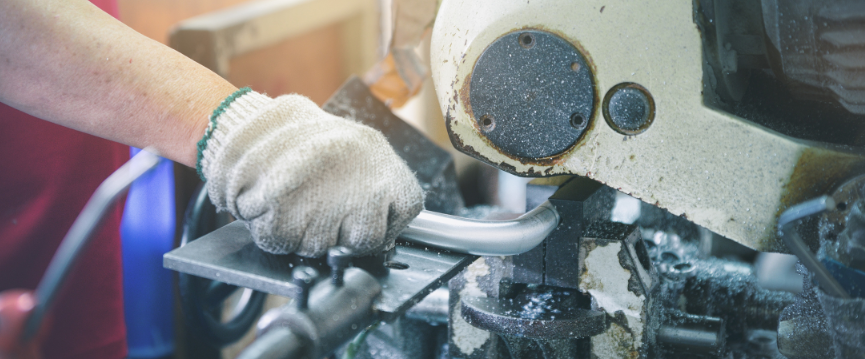
Circular Saw
In-house single-cut and double-cut circular saws available to meet different cutting needs.
Heat Treatment
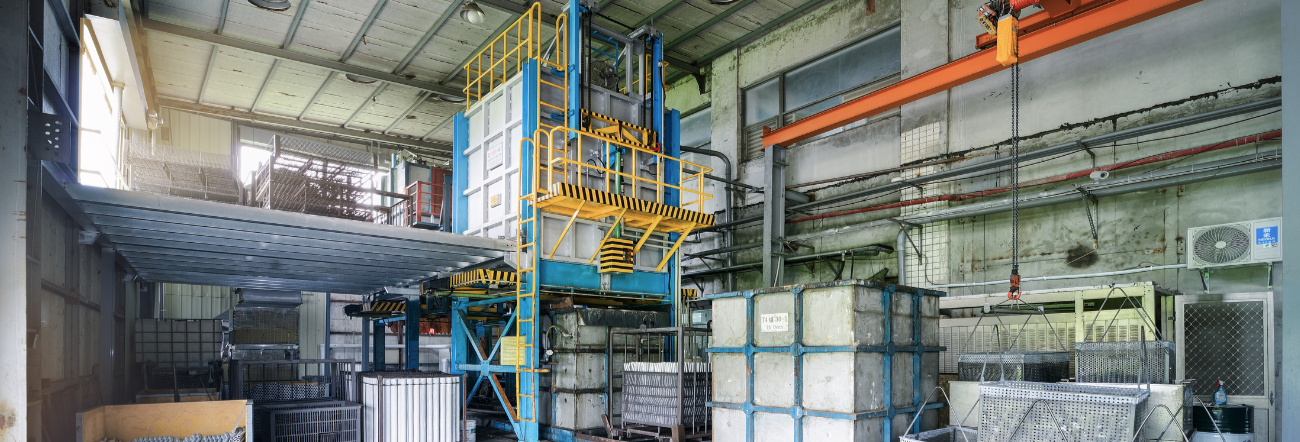
Heat treatable aluminum alloys, such as Al-Cu-Mg alloys (2XXX), Al-Mg-Si alloys (6XXX), and Al-Zn-Mg alloys (7XXX), can be precipitation-hardened to improve strength and obtain excellent mechanical properties through appropriate heat treatment procedures.
Heat treatment involves heating and cooling aluminum alloy tubing to improve its mechanical properties and durability.
Anvil has annealing furnaces (with regularly inspected/calibrated oven temperatures), T4 solution furnaces, T6 aging furnaces, and T7, which are various heat treatment methods to meet your product’s different stage processing requirements and applications.
T4
Solution Furnace / T4 Heat Treatment
Strict temperature control during the T4 solution heat treatment process ensures even distribution of solute atoms and focuses on proper soak times to achieve optimal dissolution, contributing to enhanced alloy strength and fatigue performance, ensuring the final product has excellent performance and durability.
We have extensive experience in heat treatment and can offer customized heat treatment solutions based on customer requirements and material properties. Through our heat treatment services, you can ensure that your aluminum alloy products achieve optimal results in the precipitation hardening process, satisfying the high strength and performance requirements of various applications. Our goal is to provide lasting value for your products and achieve excellent results with you.
T6
Aging Furnace / T6 Heat Treatment
T6 aging heat treatment involves various factors, including solution temperature, quenching rate (determined by quenching medium), aging temperature, holding time, and aging sequence. We will customize the best T6 aging heat treatment plan based on your needs and product characteristics, ensuring optimal performance.
CNC Machining
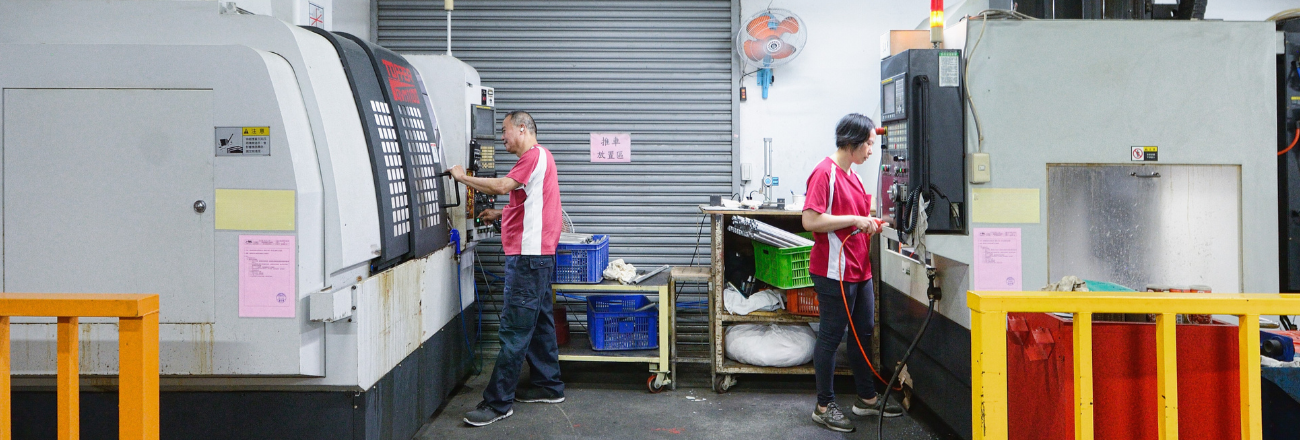
It efficiently completes tasks, saving labor costs and shortening the production cycle, thereby achieving higher production efficiency, better product quality, and more flexible manufacturing processes.
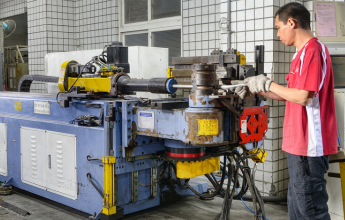
CNC Tube Bender / NC Tube Bender
▲The CNC tube bender uses computer numerical control technology and operates through pre-programmed instructions and control systems. It achieves higher automation and precision, with greater bending accuracy and repeatability. Operators can input bending parameters and graphic designs through the computer interface, completing tube bending via automated control.
▲The NC tube bender is also a numerically controlled tube bending machine, but compared to CNC, its control system and operation methods are relatively simpler. NC tube benders typically operate using pre-set numbers and parameters and involve less complicated programming and graphic design. Operators usually control the machine for bending through buttons, switches, or manual operations.
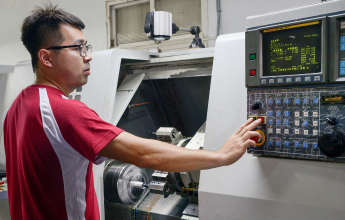
CNC Lathe / Conventional Lathe
▲Traditional lathes are driven by electric motors, which turn the main spindle, rotating the workpiece clamped on it. A cutting tool fixed on the tool rest performs the turning. Mainly used for machining round tubing pieces, the operations include facing, inner and outer diameters, tapering, drilling, reaming, offset, knurling, parting, grooving, and threading.
▲Anvil invests in "Computer Numerical Control" CNC lathes for machining, using CAD/CAM software to control the machine's movement. CNC lathes gradually replace traditional lathes, offering easy loading and unloading, doubled productivity, and significantly enhanced part precision. The technology minimizes human errors in large-scale lathe machining and serves various industries like aerospace, bicycles, and motorcycles, providing precision OEM and ODM services.
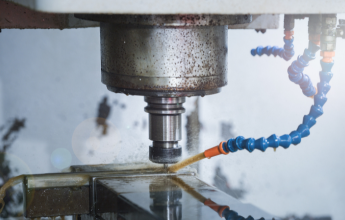
CNC Milling Machine
Drill
Vertical Drilling Machine
Mark
Roll Marking Machine
knurl
Knurling Machine
Cham-
Chamfering Machine
Grinding and Polishing
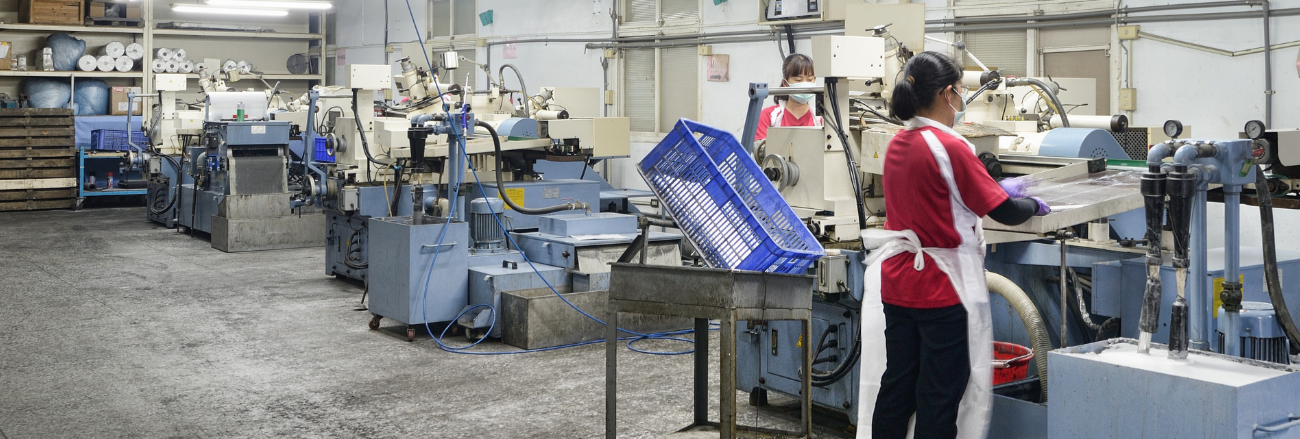
Hone
Honing Machine
Honing aims to improve machining precision, including size accuracy, roundness, cylindricity, and surface roughness. It ensures stable machining precision and produces a unique cross-hatched pattern on the product surface, enhancing lubrication.
Compared to internal diameter grinding, honing uses lower rotational speeds and smaller cutting amounts, avoiding harm and internal stresses on the product surface. Honing offers high precision, stability, shorter processing time, and longer tool life.
Grind
Tube Grinding Machine
The machining action of a grinding machine is known as grinding. It uses grinding tools to remove excess material from the workpiece to achieve the desired shape, dimensions, and machined surface. The sharpening of cutting tools and the precise manufacturing of mechanical parts all rely on grinding work. Grinding is also a part of precision machining.
Grind
Centerless Grinding Machine
Anvil specializes in manufacturing aluminum alloy tubular (hollow) products. Due to the thinner tube walls, considerable skill and conditions are required to maintain dimensions and "improve surface roughness" during grinding. Our centerless grinding services focus on technician operation and the use of high-quality grinding wheel consumables imported from Japan, providing reliable centerless grinding services for aluminum alloy tubing pieces based on your process needs.
Polish
Polishing Machine
To reduce scratches and improve surface roughness, we offer an additional mirror-like polishing process for aluminum alloy tubing pieces after grinding and before hard anodizing. This not only enhances surface roughness but also makes it easier to spot any surface defects, ensuring the quality of anodized tubing pieces. Tubing pieces that have undergone anodizing cannot be reworked; hence, grinding and polishing is an important step before coloration.
Inspection Equipment
Precision Instruments
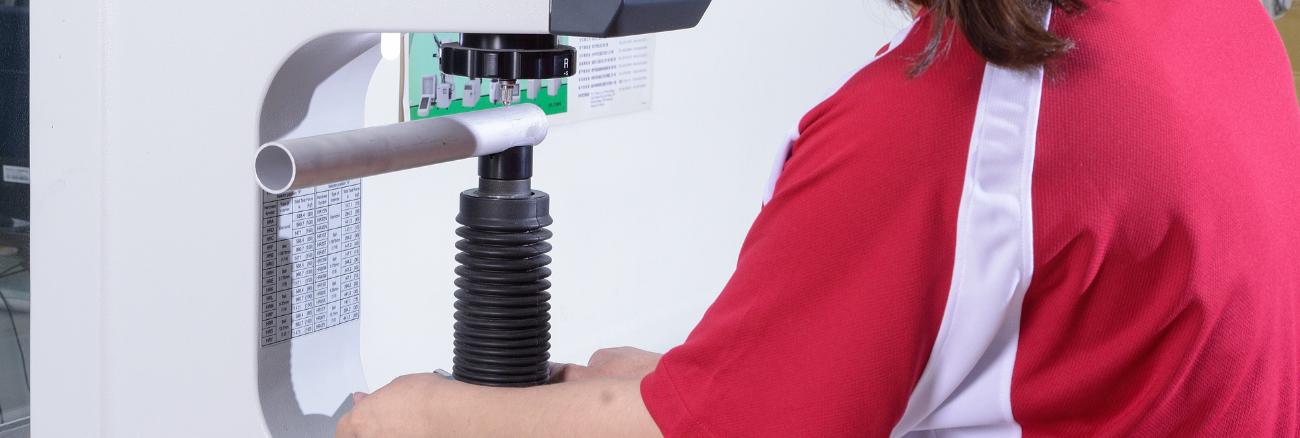
EC
EC Meter
Applications of the conductivity meter include:
▲Material identification/metal sorting
▲Heat treatment identification
▲Thermal damage measurement
▲Non-conductive coating thickness measurement
Hard
Rockwell Hardness Tester
Rough
Surface Roughness Measuring Instrument
Strength Testing
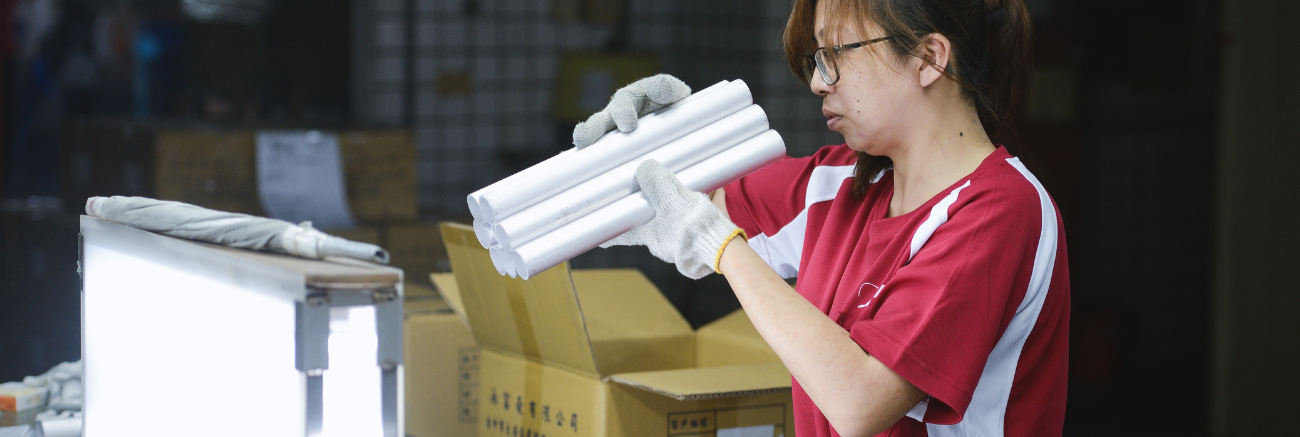
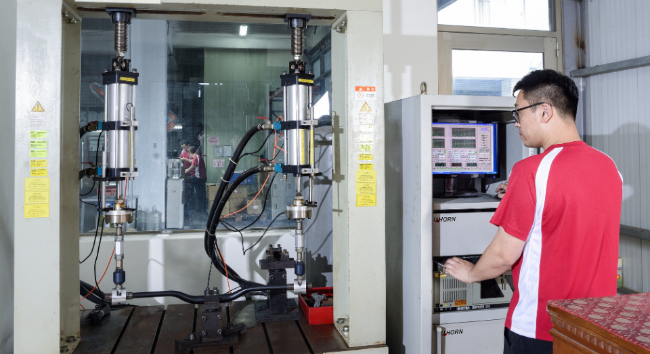
2CH Gantry-type Pneumatic Vibration Testing Machine
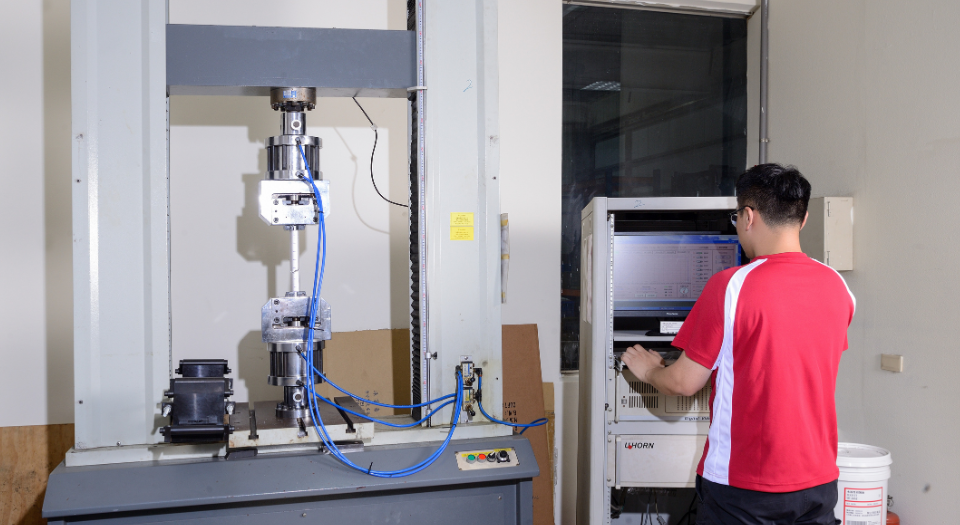
Tensile and Compression Testing Machine
Key features include:
▲Versatility: Capable of performing various types of tests to adapt to different material needs.
▲Data Logging: It can record test data for subsequent analysis and evaluation.
Metallography Lab
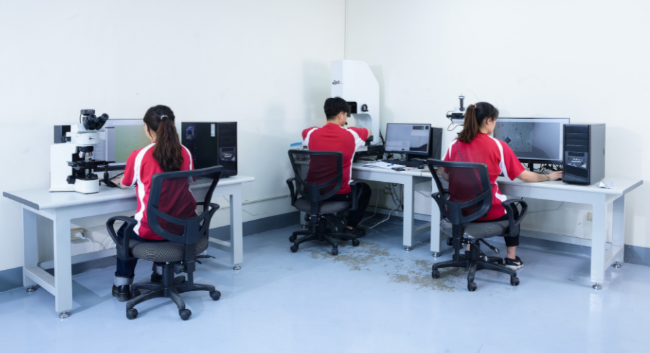
Metallographic Science
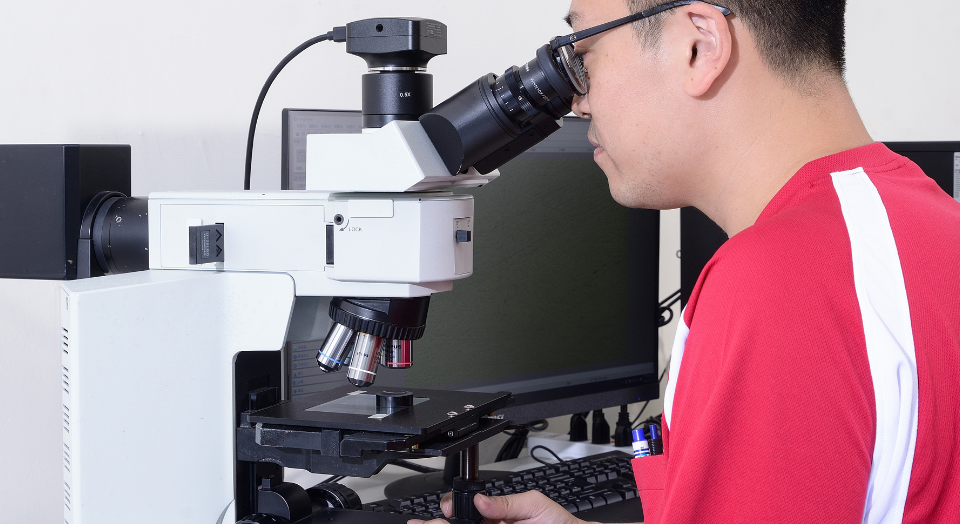
Common metallographic tests include:
▲Heat treatment quality inspection
▲Material microstructure inspection and assessment
▲Low magnification defect inspection
▲Metal hardness (HV, HRB, HB) measurement
▲Grain size rating
▲Inclusion content measurement
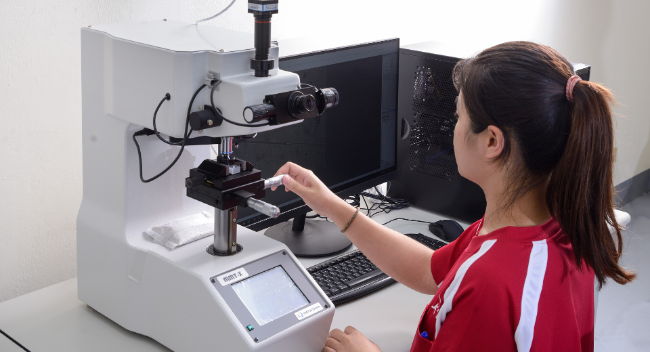
Common metallographic material analysis or microscopic structural analysis applications:
▲Cracks and defects
▲Size, shape, and distribution of inclusions
▲Weld and Heat-Affected Zones (HAZ)
▲Anodizing thickness
Metallography Testing Procedure (For Aluminum Alloys)
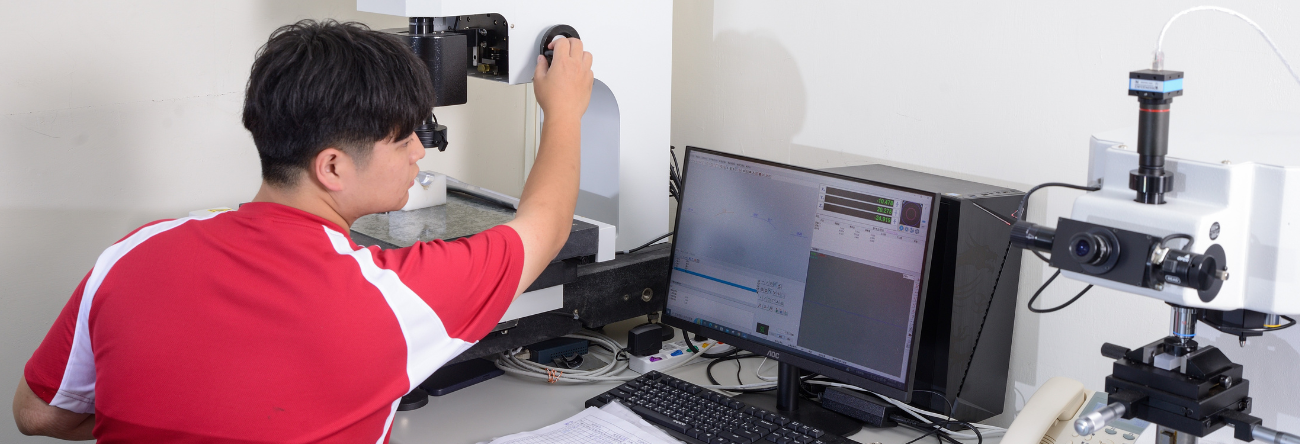
▲Select the sampling location and inspection surface, taking into account the characteristics and processing methods of the sample, and the selected area must be representative.
2.Mounting
▲If the sample size is too small or the shape is irregular, it needs to be mounted or held with fixtures.
3.Coarse Grinding -> Fine Grinding
▲The purpose of coarse grinding is to flatten the sample and shape it appropriately.
▲The purpose of fine grinding is to eliminate the deeper scratches left by coarse grinding, preparing for polishing.
4.Polishing -> Etching
▲The aim of polishing is to remove fine grinding marks or scratches, resulting in a bright, scratch-free mirror surface.
▲To observe the sample's structure under a microscope, metallographic etching is required.
5.Metalloscopy
▲Observe the "grain size" of the material; grain size has a direct correlation with the material's mechanical properties. Quantitative analysis of grain size can provide an accurate evaluation basis. The number of grains per unit area in metallography is related to the grain size, which has a decisive impact on the metal's tensile strength, material hardness, and ductility.